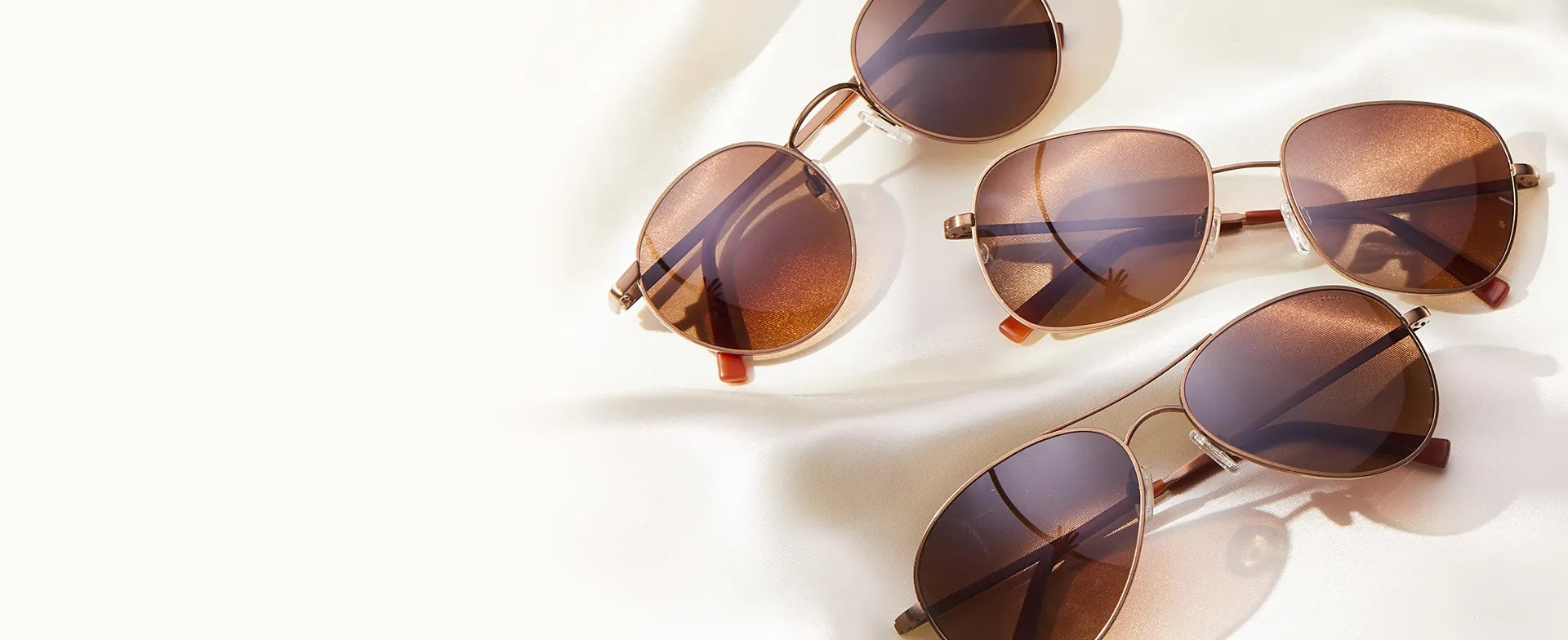
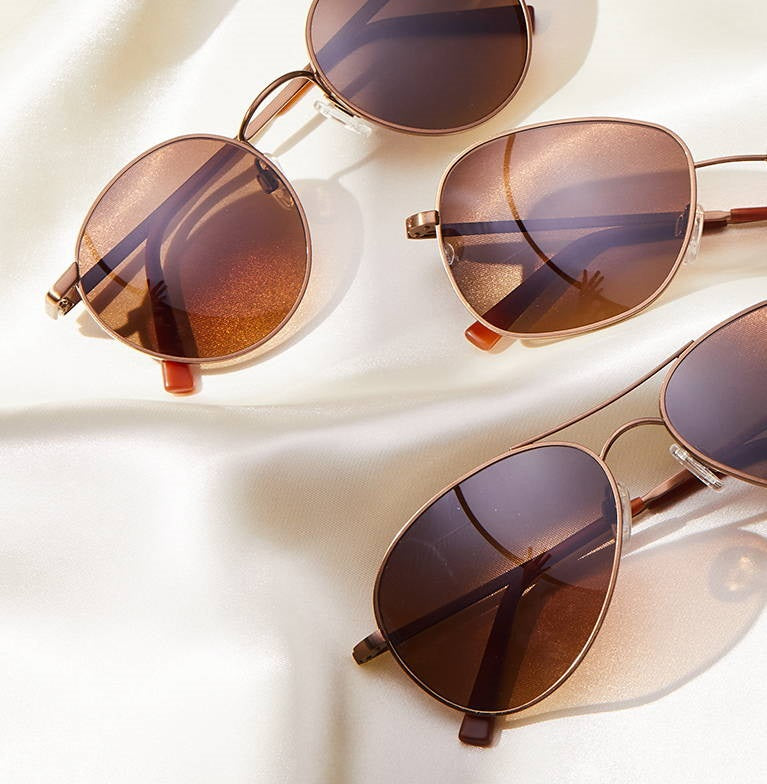
SUNGLASSES STYLES
From the Iconic Aviator to the Retro P3, we have designed a frame shape to suit every face shape and personal style. Designed with purpose, built with excellence in the US.
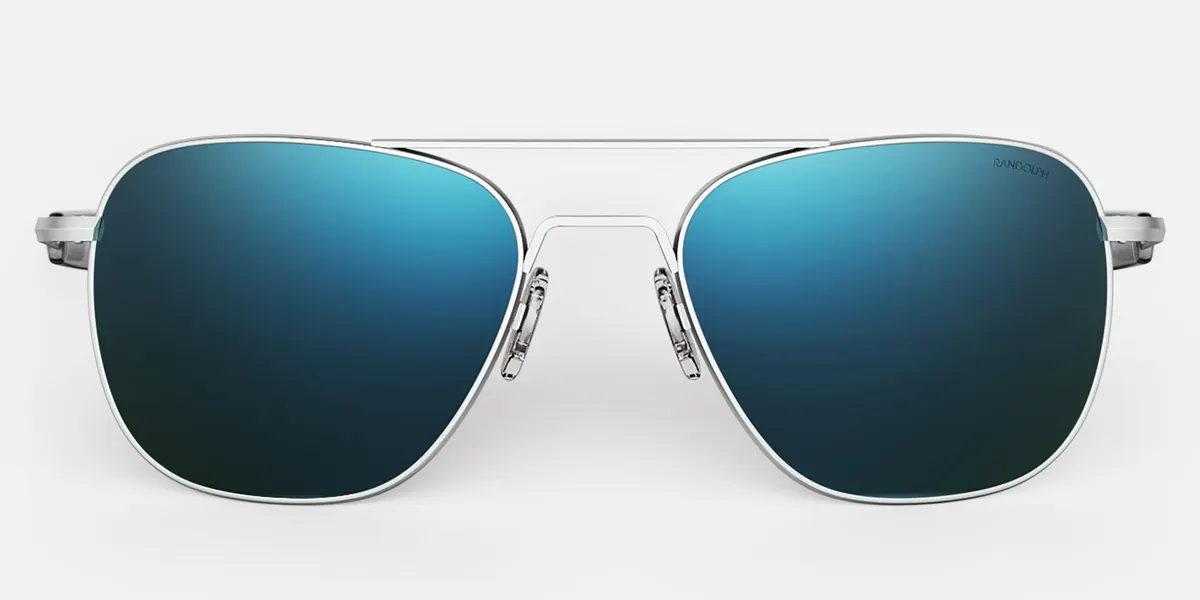
AVIATOR
Originally built for the U.S. Military, the iconic Randolph Aviator surpasses rigid military-spec standards. Standard issue since 1978, our Aviator sunglasses are battle tested and suitable for the most rigorous demands and are a superior choice for everyday use.
SHOP AVIATOR >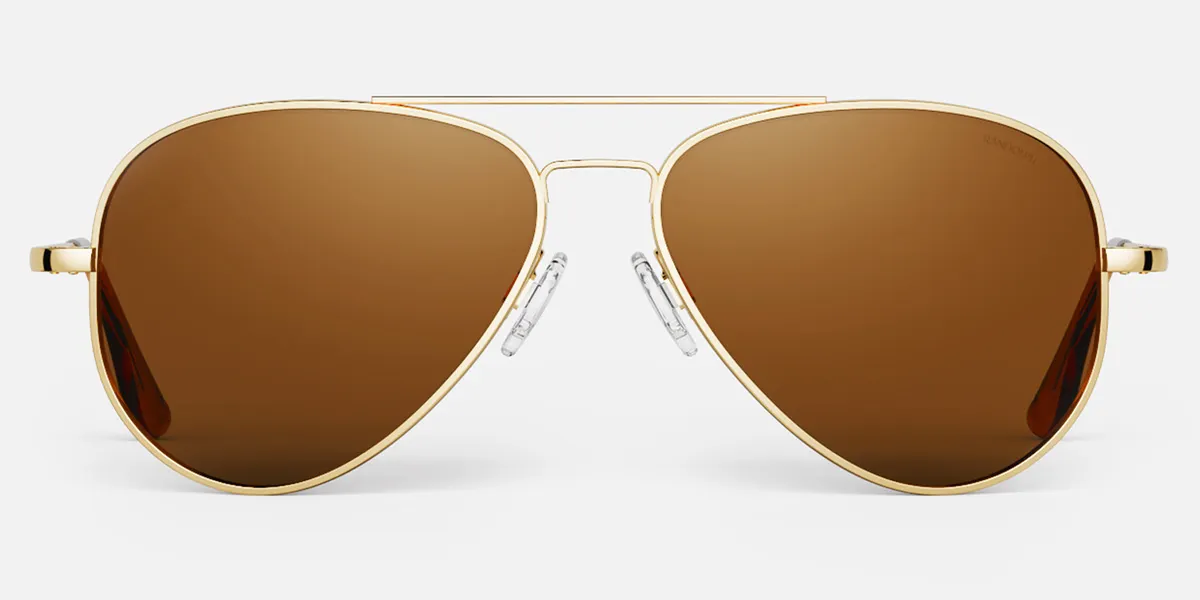
CONCORDE
Randolph Engineering offers the iconic teardrop Concorde with a style hearkening back to the original days of the aviator. The style is named after the Concorde supersonic passenger airliner, which entered service in 1976, three years after Randolph Engineering was founded.
SHOP CONCORDE>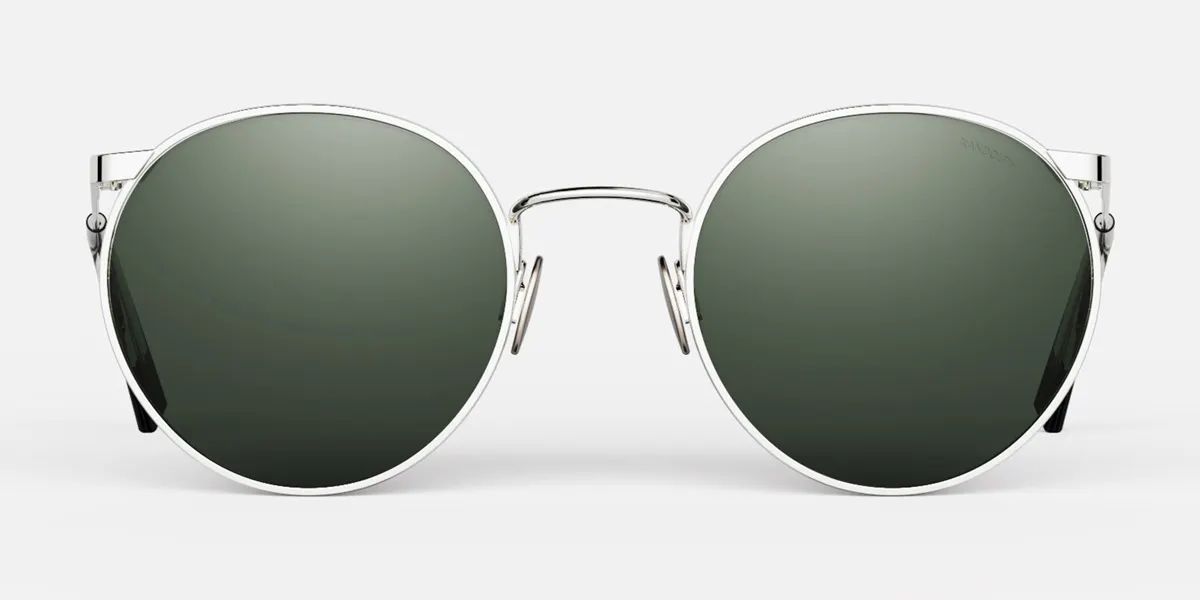
P3
This iconic retro P3 style is a favorite among those looking for a vintage and slightly edgy look. Built to meet the same military standards as our classic Aviator, they offer a playful take on our military heritage.
SHOP P3 >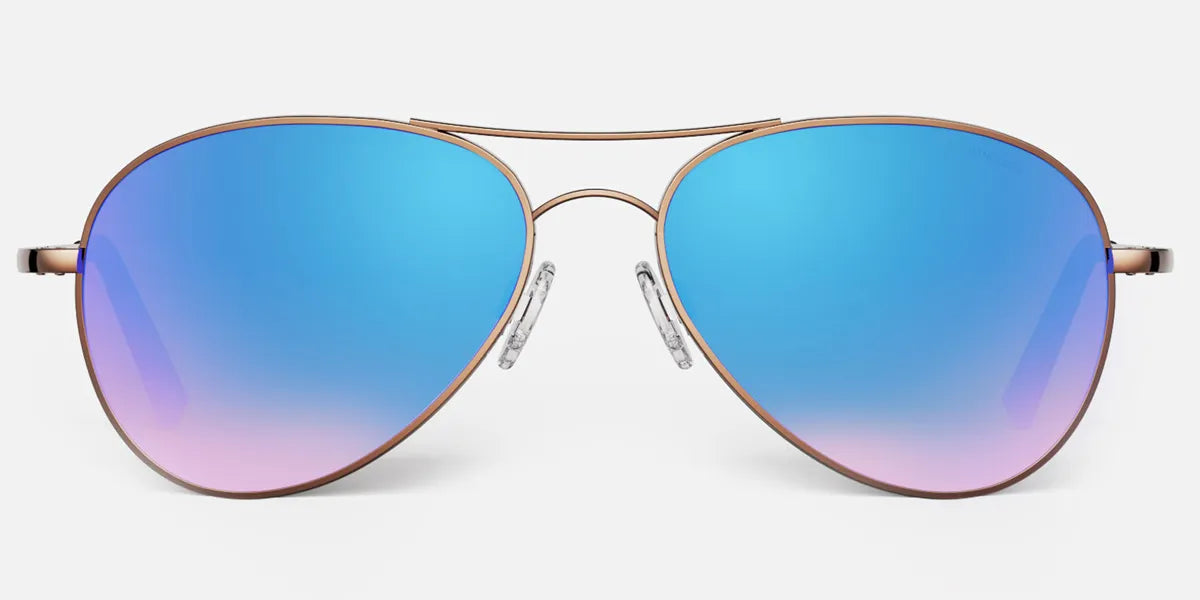
AMELIA
The Amelia, named in honor of Amelia Earhart, was Randolph’s first style dedicated to feminine fashion. While all Randolphs are unisex, the Amelia offers unique features such as a dipped brow bar to fit female faces and was released with luxury frame finishes more often found in women’s jewelry.
SHOP AMELIA >HANDCRAFTED IN THE USA
Purposefully engineered and built to last at our family-owned and operated factory.

ARCHER
The Archer embodies contemporary masculine cool. Inspired by ballooning pioneer Samuel Archer King, the Archer is all about attitude and innovation. Wrapped lenses cover a larger range of the face than our classic Aviator styles, preventing as much light as possible from entering the eye.
SHOP ARCHER >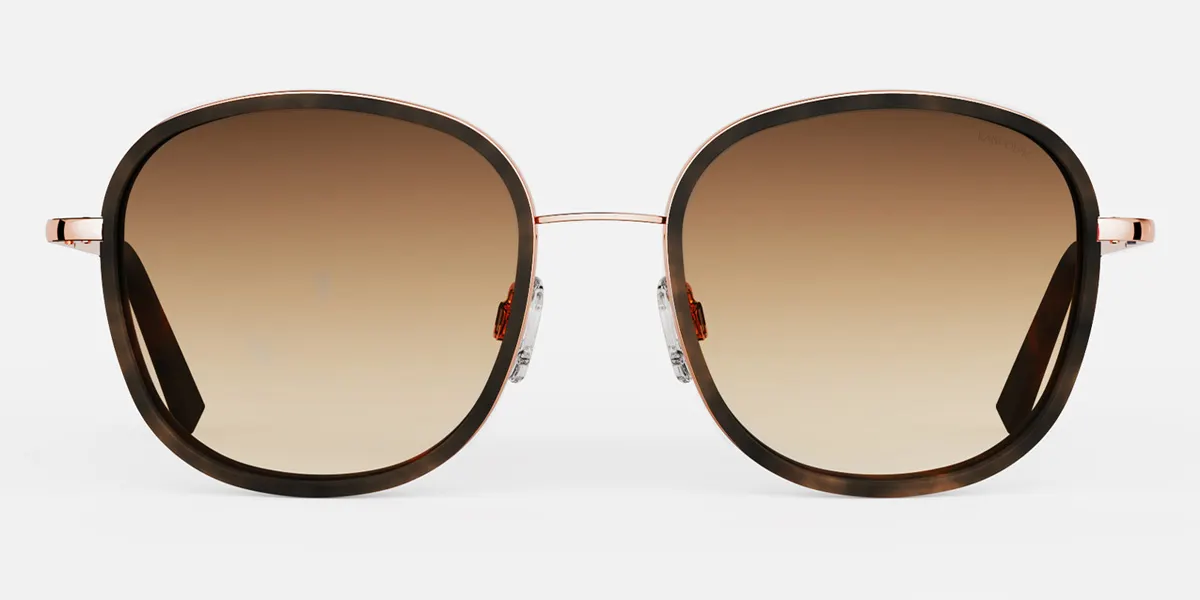
ELINOR FUSION
A perfect frame for almost every female face shape. Named after Elinor Smith, aviation record breaker, this iconic lens shape also pays homage to Jackie O and her classic style. Fusing the strength of metal with the style and personality of acetate.
SHOP ELINOR >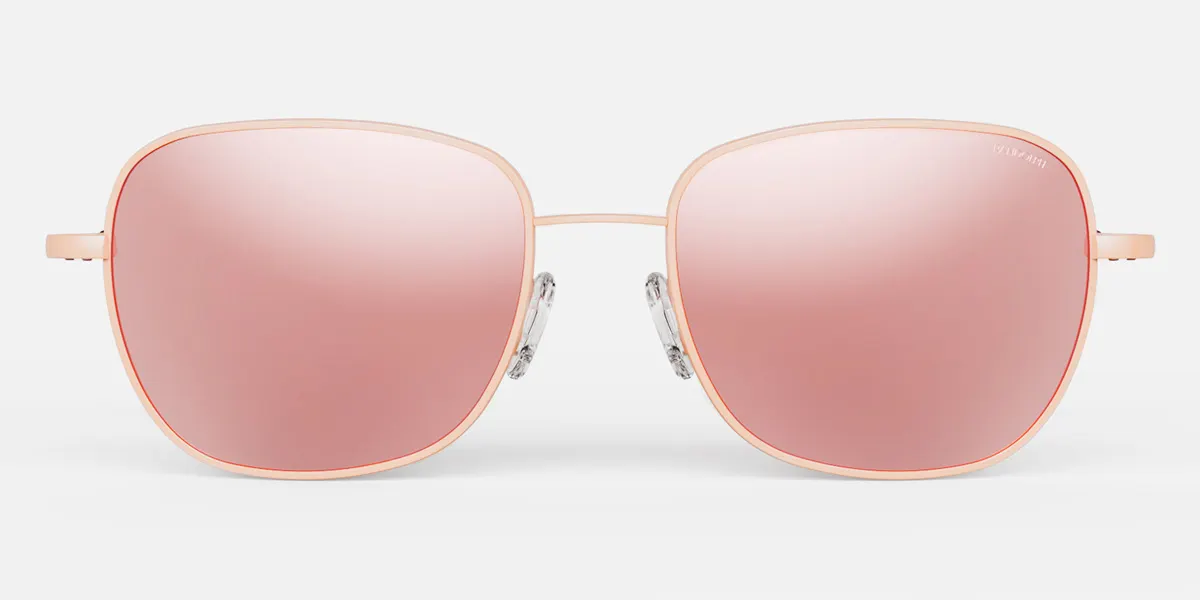
CECIL
Named after Cecil “Teddy” Kenyon, a test pilot for Grumman Aircraft during WWII, Cecil is an oversized square shaped frame with a lightweight bridge and classic streamlined styling. Cecil brings a touch of old hollywood glamour to the aviation eyewear space with this Jackie O’ style frame.
SHOP CECIL >
SPORTSMAN
Similar to the Concorde, the Sporstman has been updated with an additional brow bar featuring soft acetate padding, which perfectly matches the skull-style temple tips. The design adds stylish and bold personality to the frame with a horizontal, chromatic-patterned piece on the brow.
SHOP SPORTSMAN >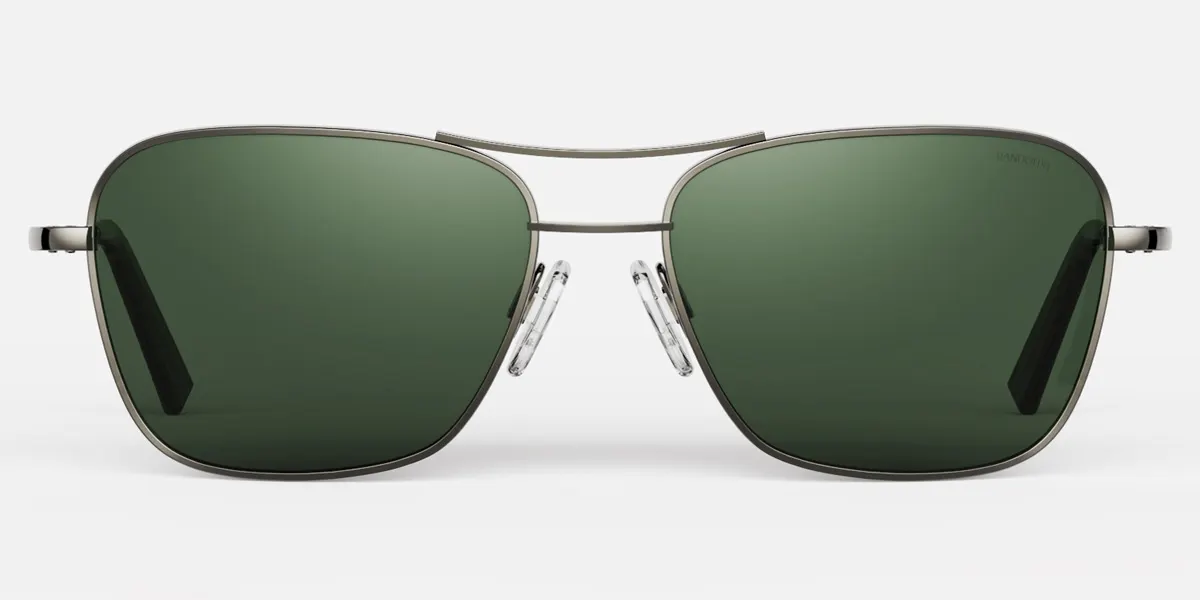
CORSAIR
The F4U Corsair, flown in combat by U.S. Navy, Air Force, and Marine pilots, was the inspiration for this high-performing and comfortable style. Built to meet US Military Standards, the Corsair is distinguishable by it’s subtle dip to the brow bar that gives the rectangular frame a strong aerodynamic look.
SHOP CORSAIR >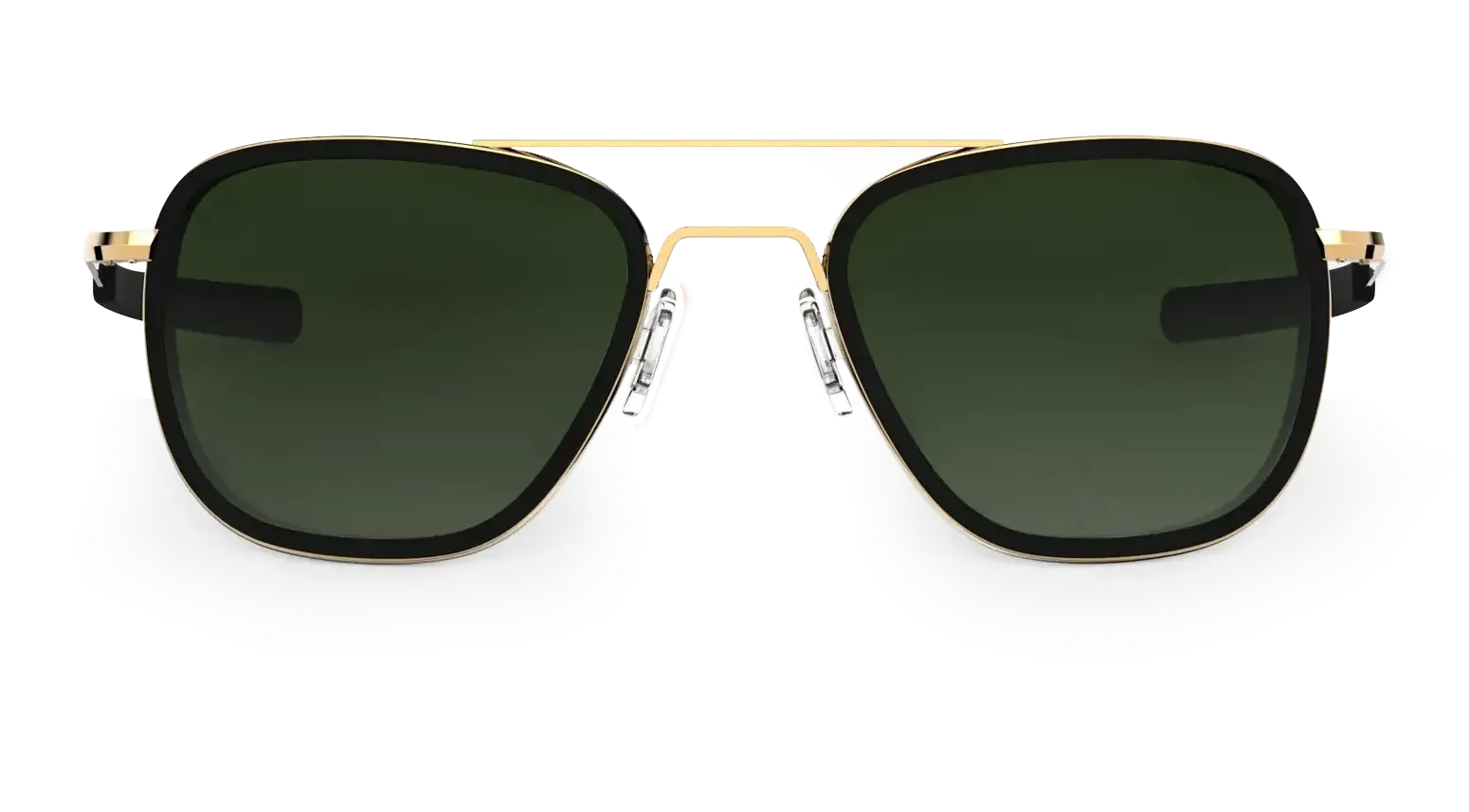
AVIATOR FUSION
Our iconic Aviator style, reinvented with the fusion of heritage metalcraft, jewelry-quality finishes and handmade Mazzucchelli acetate.
SHOP AVIATOR FUSION >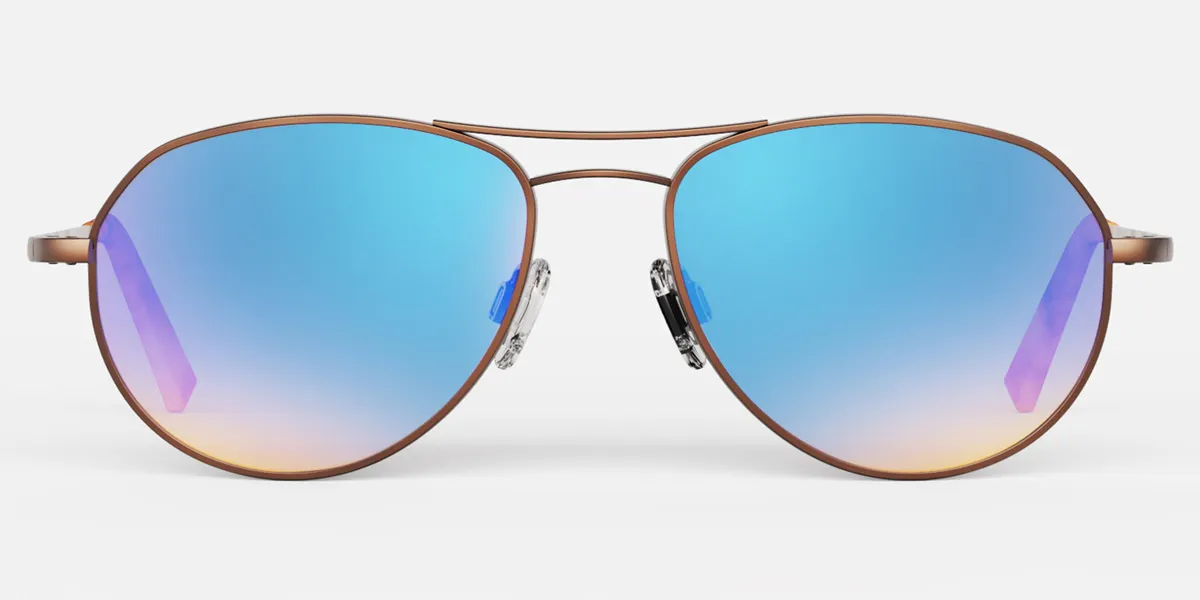
THADEN
A frame purposefully engineered to fit smaller faces, Thaden features a slight teardrop lens shape with all-new unique, angular twist on the outer top edges. The slight geometric edge is subtle and quietly breathes new life into a timeless teardrop style.
SHOP THADEN >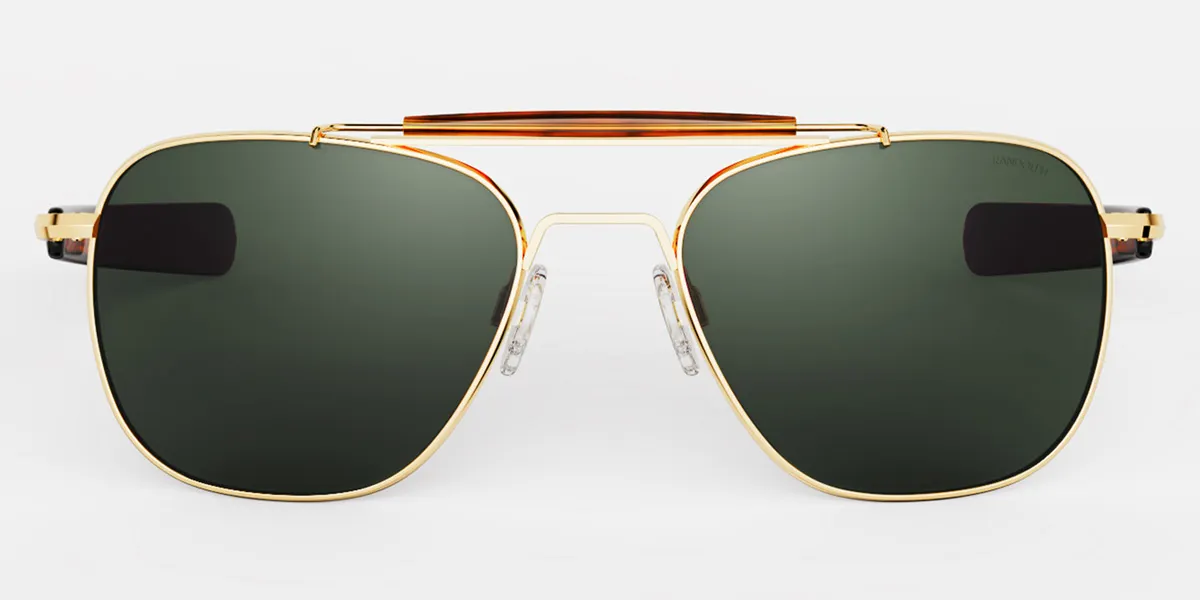
AVIATOR II
How do you improve on perfection? We’ve taken our authentic Aviator, originally built for the U.S. Military, and reinvented it to include an additional sweat bar for added comfort and a distinguished look. The acetate sweat bar details perfectly match our classic bayonet temples with a subtle pattern.
SHOP AVIATOR II >SINCE 1973
Timeless styles. Reimagined classics.
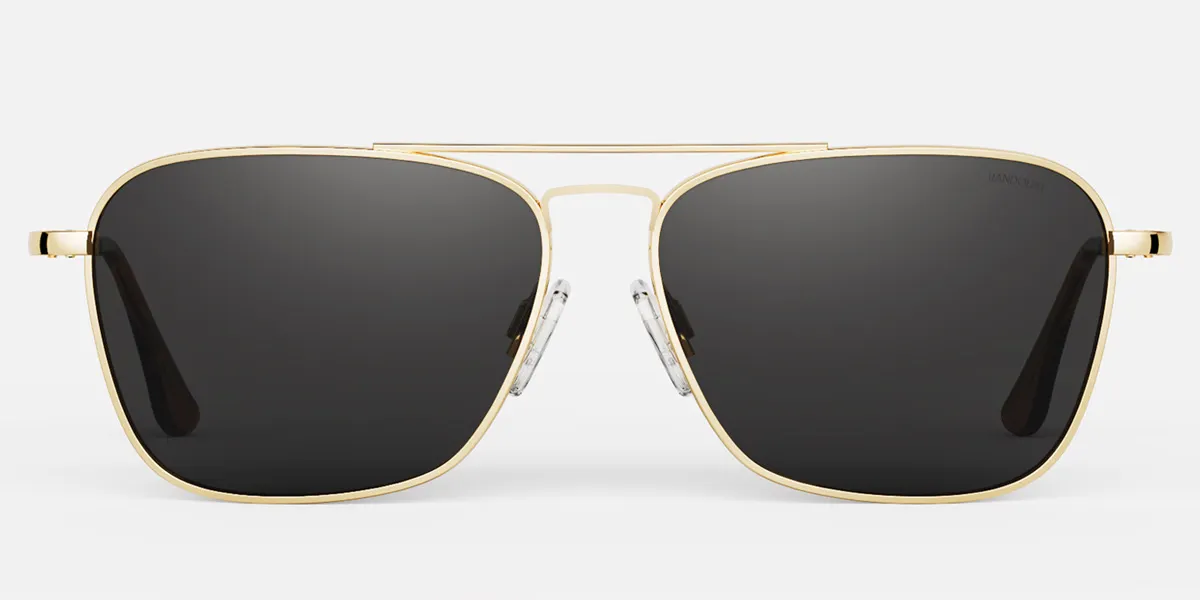
INTRUDER
Named after the A-6 Intruder, a twin-engine, mid-wing, all-weather attack aircraft, the Intruder is built to meet the same military standards as our classic Aviator, with a more rectangular shape and close-sitting lenses that provide additional coverage.
SHOP INTRUDER >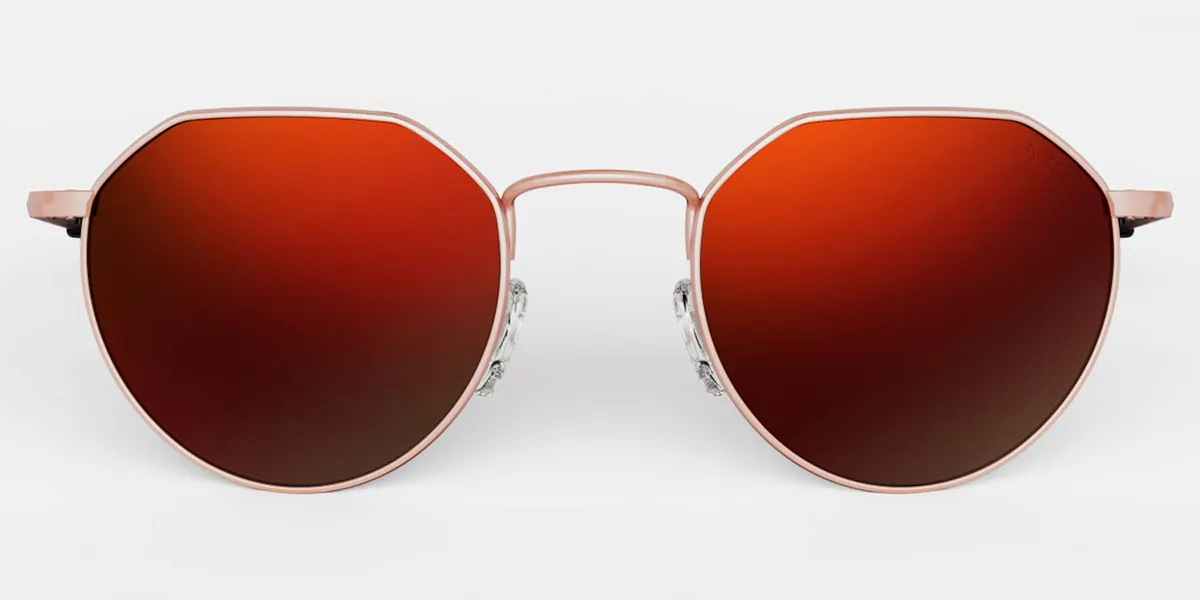
HAMILTON
This lightweight geometric frame is fashion forward yet vintage in design, with it’s round hexagonal shape dating back to the 1920’s. We’ve reinvented the Hamilton style and updated it with inspiration from our retired Franklin and Jefferson shapes.
SHOP HAMILTON >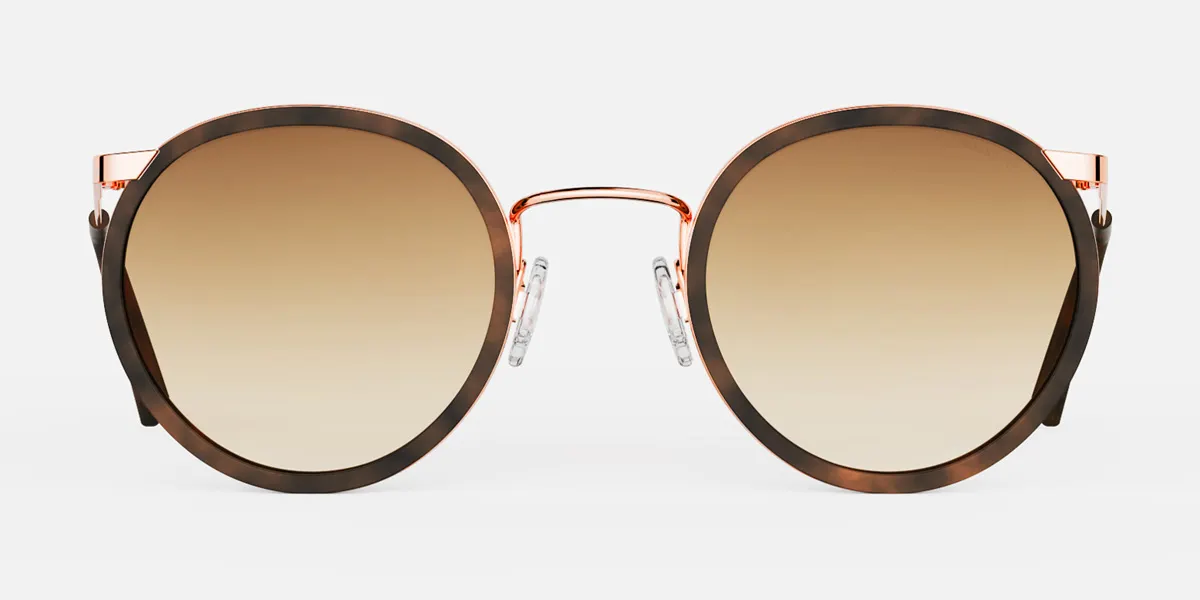
P3 FUSION
A reinvention of our classic P3 style, we added the P3 Fusion to our collection to add a little extra fun. The P3’s premium finishes and SkyForce Air™ lenses are complimented perfectly by the soft Mazzucchelli acetate inlays of the Fusion Collection.
SHOP P3 FUSION >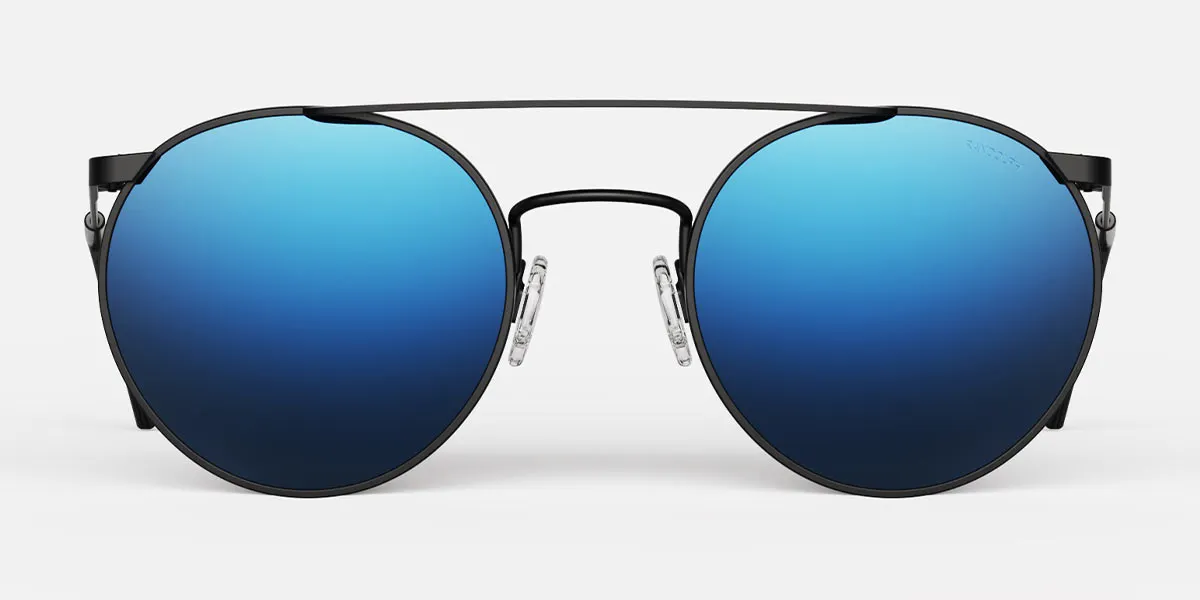
P3 SHADOW
The P3 Shadow is a formidable design, revolutionizing the standard P3 style with a strong, unique brow bar. Adopt a military chic look for both a fashionable and durable style that’s stood the test of time.
SHOP P3 SHADOW >